BogusSVO
Well-known member
2G 7 Bolt Oil Squirter Block off
It is common practice in a rebuild to block the oil squirters that are fed from the mains of the 2g 7 bolt blocks.
This style of squirter can rob oil from the main bearings if they fail open, or become dislodged from the press fit bores they are installed in.
There various methods used to do this, several ways to plug the squirter bores, some even weld.
The tools needed
• Long drift
• Hammer
• ¼ x 20 tap
• Tap driver
• Can of brake clean
• Compressed air
• Loc-Tite “Green”
• 4 set screws ¼ x 20 x 1/2L
• Allen wrench to fit the set screw
• Blunt chisel or flat nose punch
First thing to do is to knock out the oil squiters,
Take the long drift and hammer and knock the squirters out toward the mains.
Now that all 4 squirters are out. (When I knocked one out it bounced on the floor )
Now the block is placed on end, timing belt side down.
Now with the 1/4x 20 tap and tap driver and tap the squirter bores (NOT the main oil feed galley)
The trick here is NOT to tap all the way through, when the set screw is installed, toy want it to have a seat to lock into.
Now blow the tap chips out with compressed air
Now a squirt of brake clean to remove any oil
Then blow dry with more compressed air.
Next place the set screw on the allen wrench and add a drop of green loc-tite
Now screw the set screw in place.
Make sure the set screw is flush or below the floor of the oil groove. If it is above the floor of the oil groove, it will obstruct the oil flow behind the bearing.
Next take the blunt chisel or flat nose punch and peen over the edge of the block casting to help lock the set screw in place.
Now repeat on the other 3 oil squirter bores.
It is common practice in a rebuild to block the oil squirters that are fed from the mains of the 2g 7 bolt blocks.
This style of squirter can rob oil from the main bearings if they fail open, or become dislodged from the press fit bores they are installed in.
There various methods used to do this, several ways to plug the squirter bores, some even weld.
The tools needed
• Long drift
• Hammer
• ¼ x 20 tap
• Tap driver
• Can of brake clean
• Compressed air
• Loc-Tite “Green”
• 4 set screws ¼ x 20 x 1/2L
• Allen wrench to fit the set screw
• Blunt chisel or flat nose punch
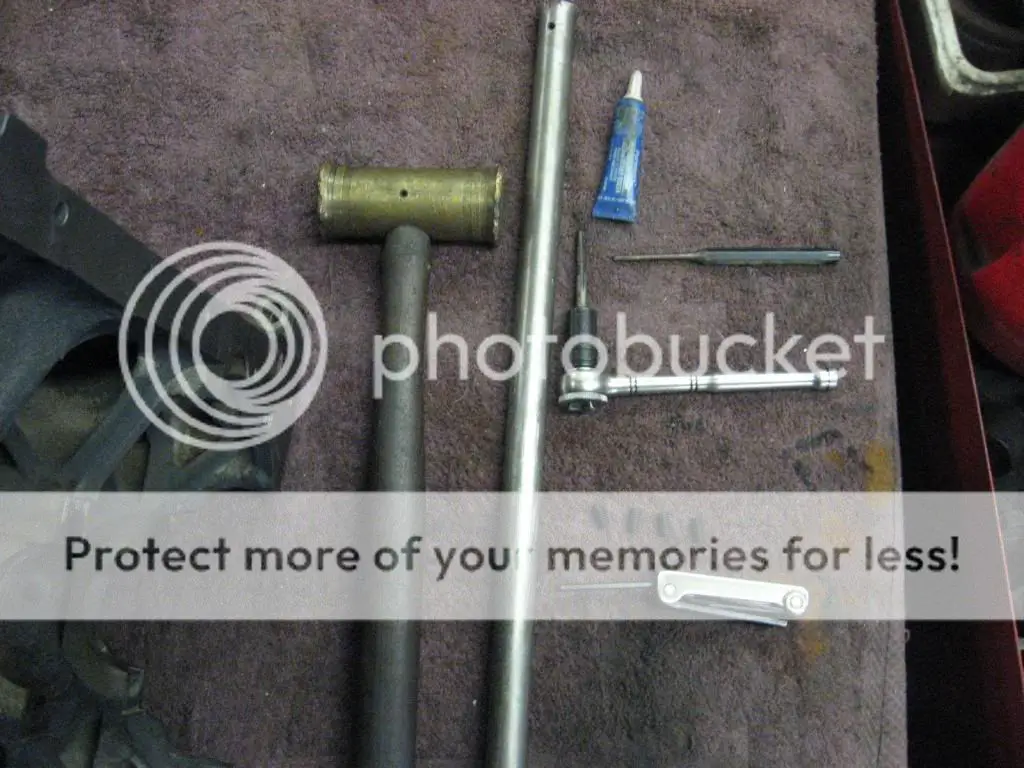
First thing to do is to knock out the oil squiters,
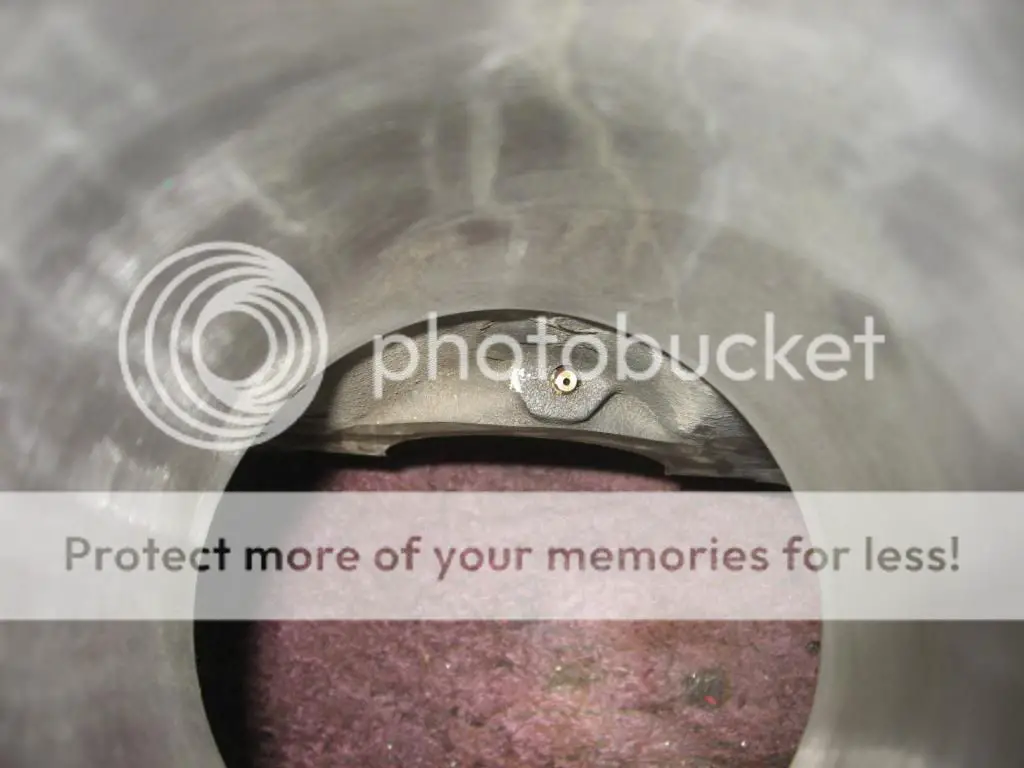
Take the long drift and hammer and knock the squirters out toward the mains.
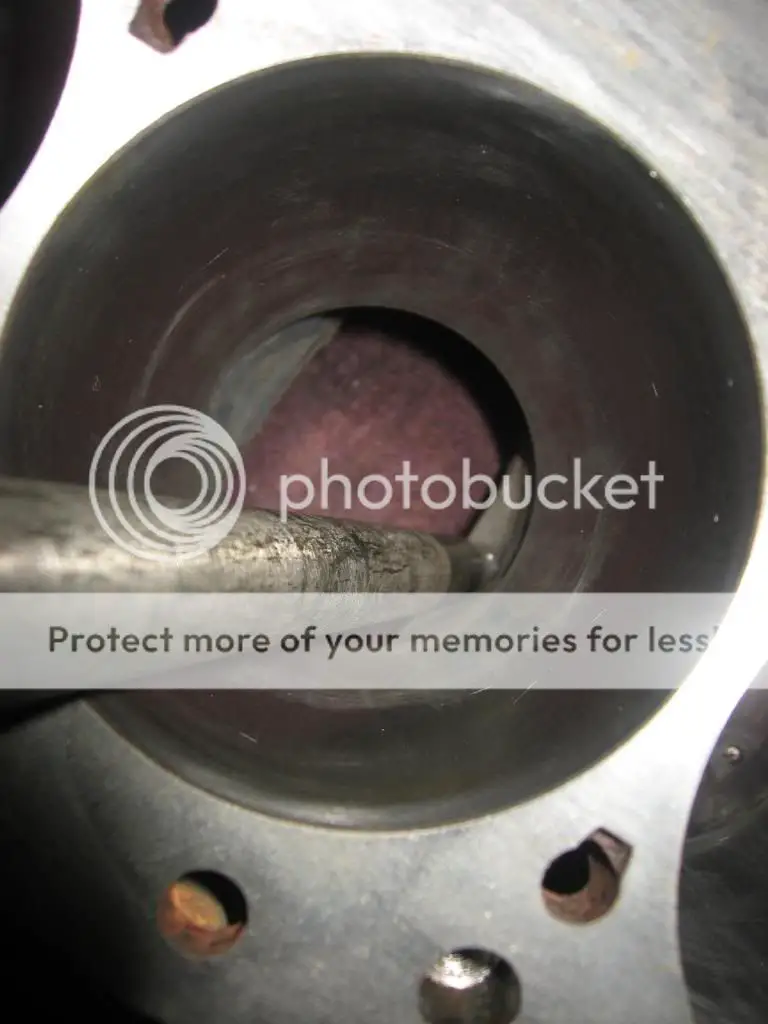
Now that all 4 squirters are out. (When I knocked one out it bounced on the floor )
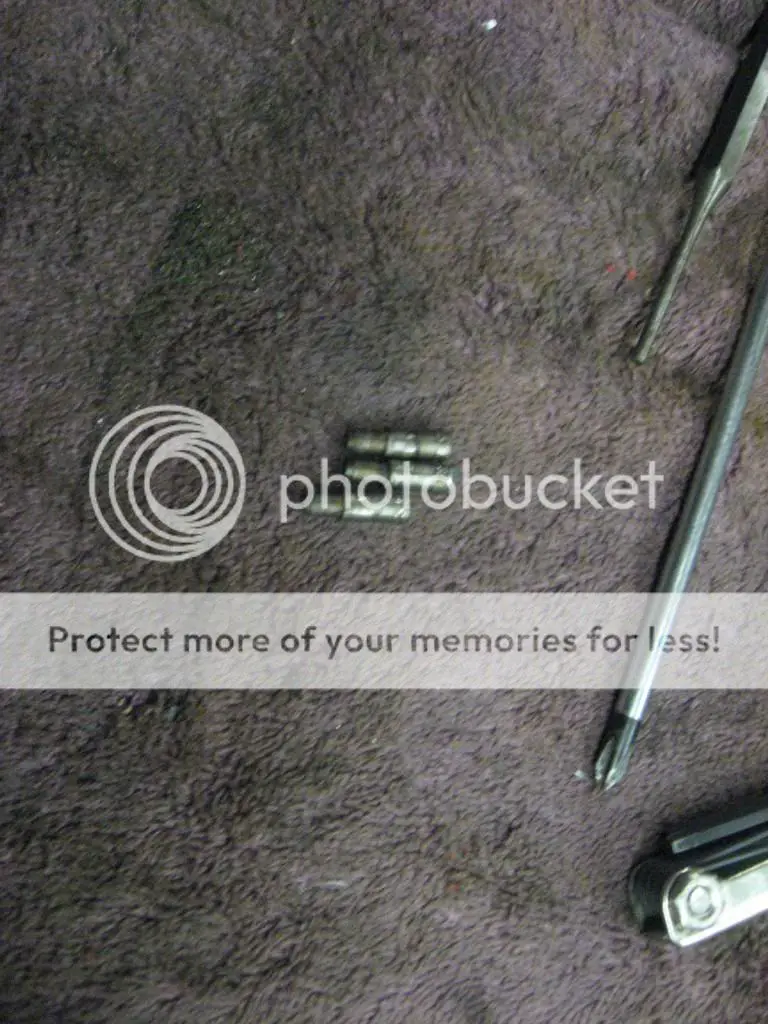
Now the block is placed on end, timing belt side down.
Now with the 1/4x 20 tap and tap driver and tap the squirter bores (NOT the main oil feed galley)
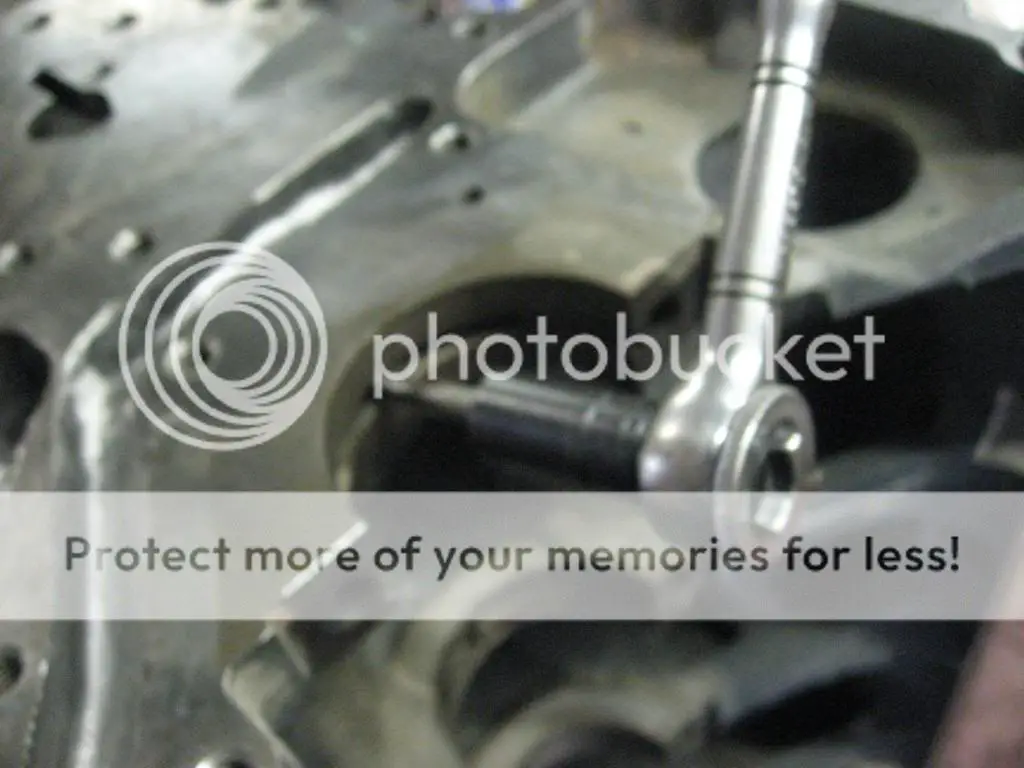
The trick here is NOT to tap all the way through, when the set screw is installed, toy want it to have a seat to lock into.
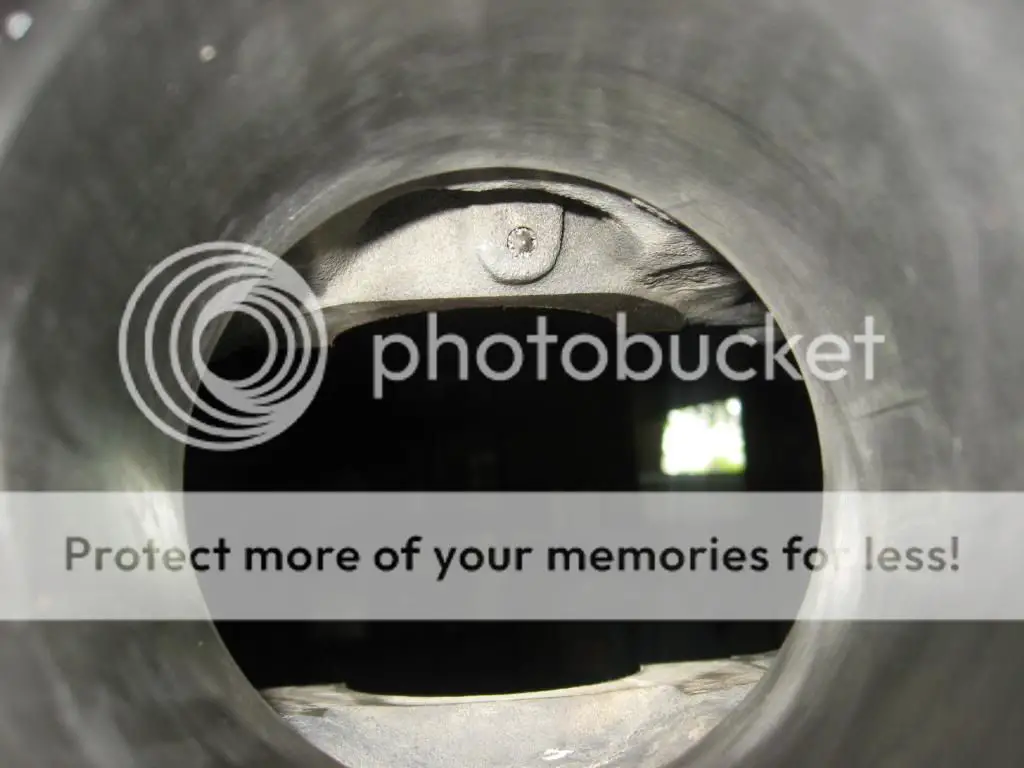
Now blow the tap chips out with compressed air
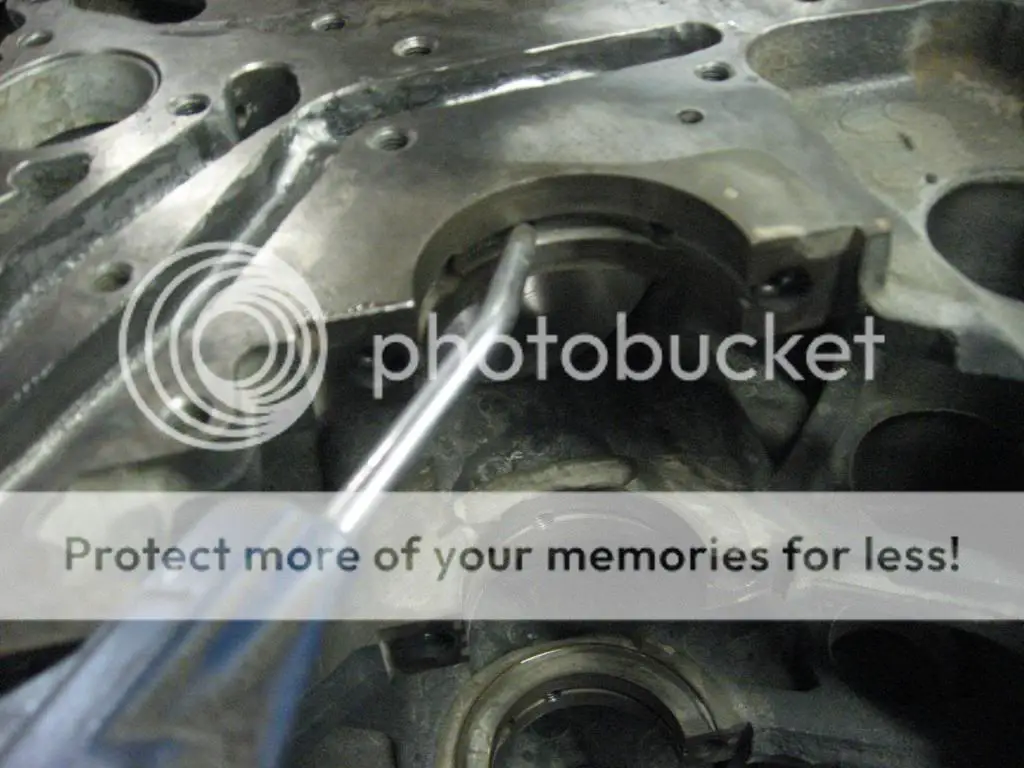
Now a squirt of brake clean to remove any oil
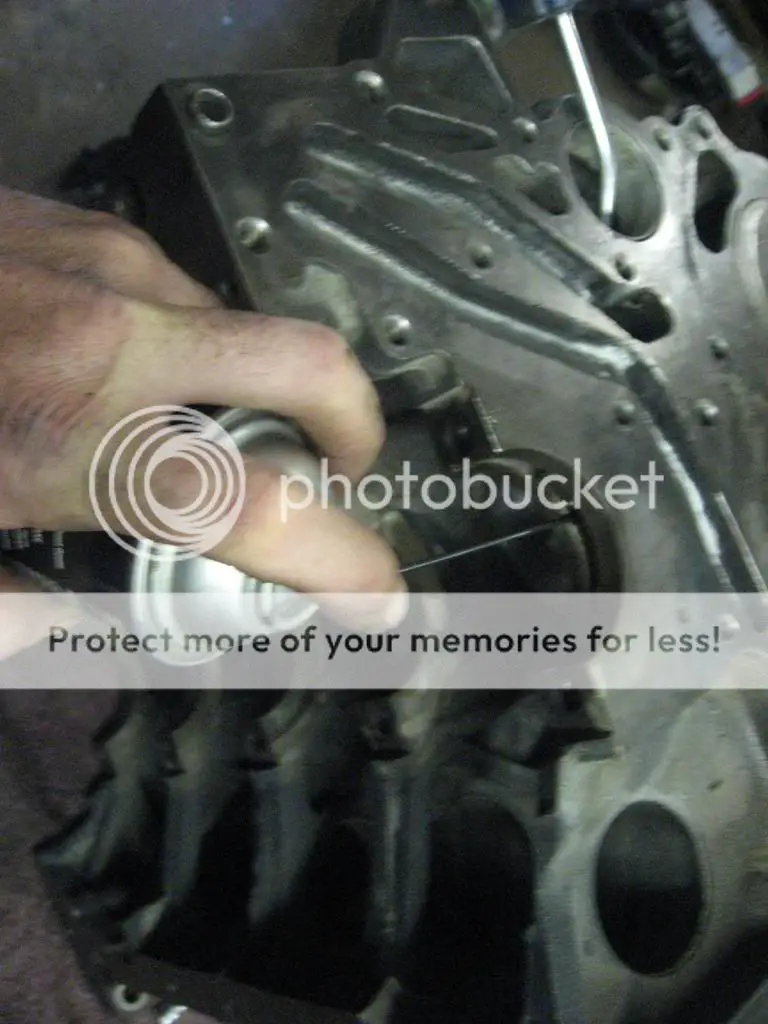
Then blow dry with more compressed air.
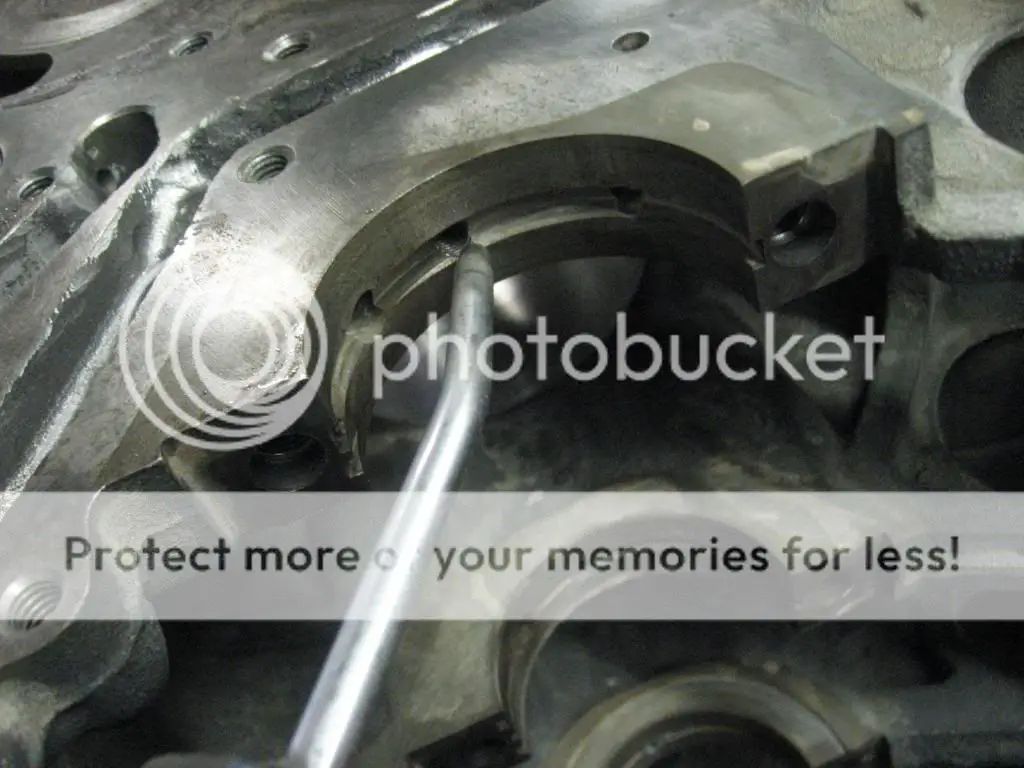
Next place the set screw on the allen wrench and add a drop of green loc-tite
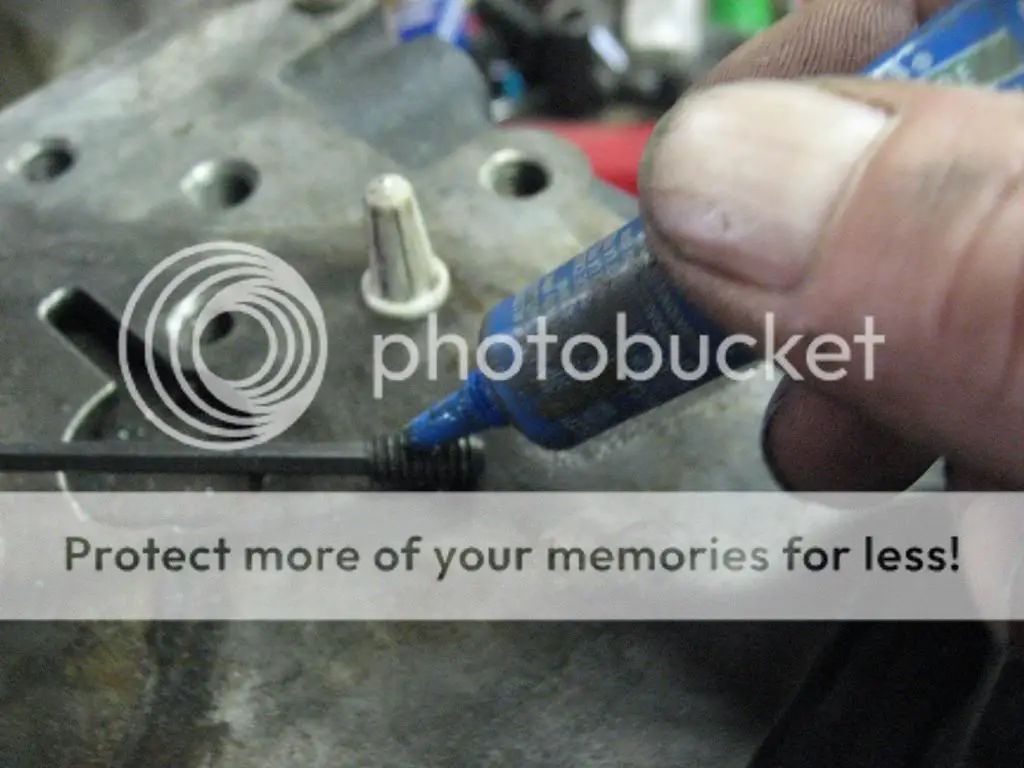
Now screw the set screw in place.
Make sure the set screw is flush or below the floor of the oil groove. If it is above the floor of the oil groove, it will obstruct the oil flow behind the bearing.
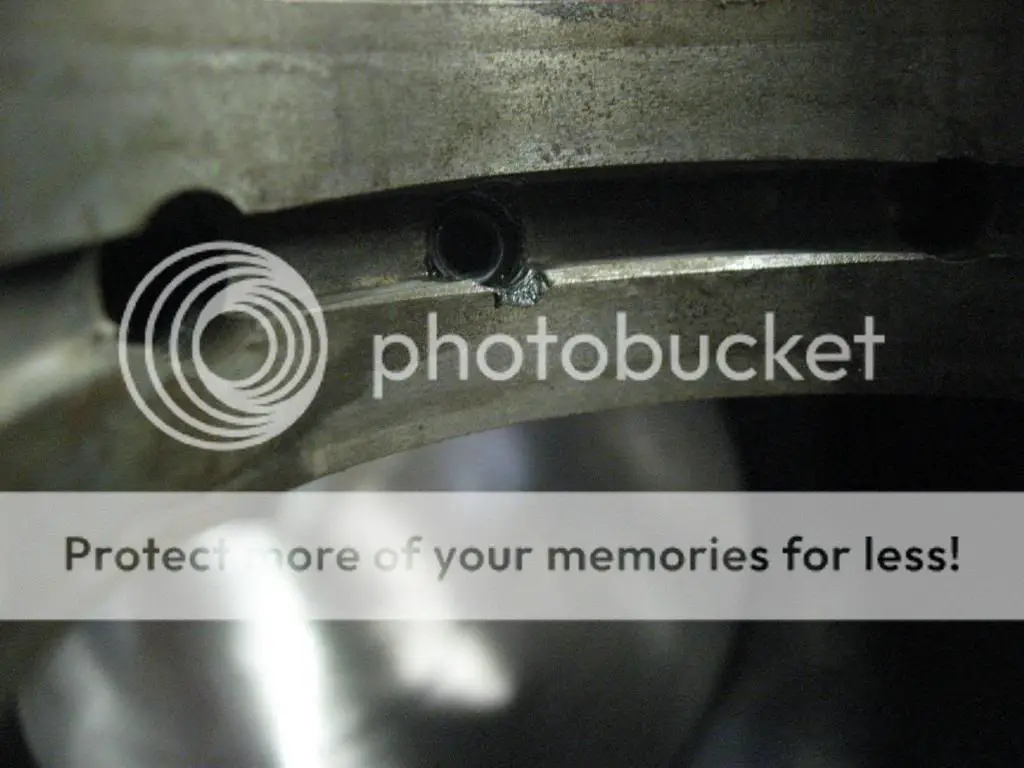
Next take the blunt chisel or flat nose punch and peen over the edge of the block casting to help lock the set screw in place.
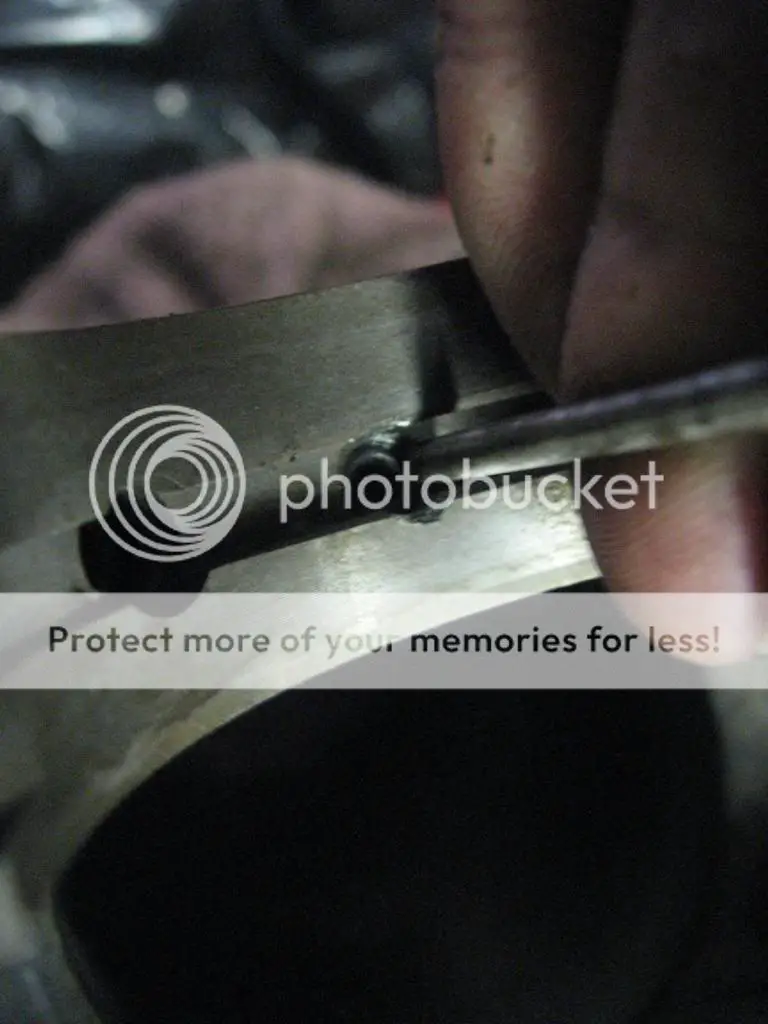
Now repeat on the other 3 oil squirter bores.